- Beranda
- Komunitas
- News
- mendirikan membuat komunitas di internet
Application of Industrial PC in Sewage Treatment Plant Monitoring
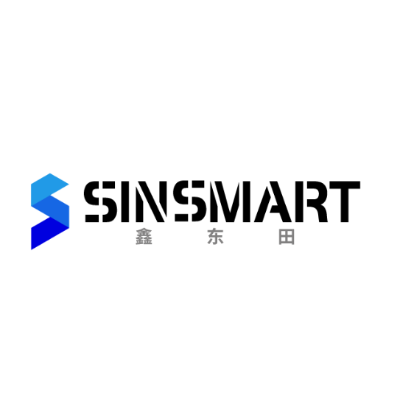
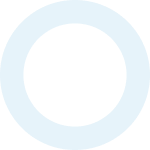
TS
sinsmarttech970
Application of Industrial PC in Sewage Treatment Plant Monitoring
Industrial PCs (IPCs) are mission-critical components in modern sewage treatment plant (STP) monitoring and control systems, providing the robust computing power needed to operate 24/7 in extremely harsh environments. Here's how they are applied:
https://www.sinsmarts.com/4u-rackmou...t-pc-computer/
[ol][li]Environmental Resilience - Core Advantage:[/li][li]Dust & Particulate Protection (IP65/IP67): Sealed enclosures prevent ingress of dust, grit, and airborne fibers prevalent in STPs, especially near screens, grit chambers, and drying beds.[/li][li][ul][li]Humidity & Corrosion Resistance: Protected against high humidity, condensation, and corrosive gases (e.g., H2S) using conformal coatings, stainless steel housings, or specialized materials. Prevents short circuits and component degradation.[/li][li]Wide Temperature Tolerance (-20°C to 60°C+): Operates reliably in unheated pump houses, hot control rooms, and outdoor enclosures without climate control.[/li][li]Vibration & Shock Resistance: Withstands constant vibrations from pumps, blowers, and heavy machinery, using solid-state components (SSDs) and ruggedized construction.[/li][li]Chemical Splash Resistance: Resists damage from accidental spills of chemicals used in treatment (coagulants, disinfectants, pH adjusters).[/li][/ul][/li][li]Continuous Operation & Reliability:[/li][li][ul][li]Fanless Design: Eliminates the primary point of failure (fans clogged by dust/humidity) and allows silent operation. Passive cooling via heatsinks or chassis dissipation.[/li][li]Industrial-Grade Components: High-quality capacitors, power supplies, and motherboards designed for long-term, stable operation under load (24/7/365).[/li][li]Extended Product Lifecycles: Components are available and supported for 5-10+ years, ensuring system stability and reducing costly re-engineering.[/li][/ul][/li][li]Data Acquisition & SCADA/HMI Hosting:[/li][li][ul][li]Sensor Interface Hub: Connect directly to a vast array of sensors monitoring:[/li][li][ul][li]Flow rates (influent, effluent, between processes)[/li][li]Level (tanks, clarifiers, wet wells)[/li][li]Pressure (pump discharge, filter beds)[/li][li]Water Quality (pH, DO, ORP, Conductivity, Turbidity, TSS, Ammonia, Nitrate, Phosphate - often via analyzers)[/li][li]Equipment Status (pump on/off, valve position, motor load)[/li][/ul][/li][li]SCADA System Host: Run the core SCADA software that aggregates data from all PLCs and RTUs across the plant, providing central monitoring and control.[/li][li]HMI (Human-Machine Interface): Serve as the operator's workstation, displaying real-time process graphics, trends, alarms, and allowing manual control interventions. Often mounted near process areas or in control rooms.[/li][/ul][/li][li]Process Control & Automation:[/li][li][ul][li]Local Control Logic: Execute complex control algorithms (e.g., aeration control based on DO, chemical dosing based on flow and pH/turbidity) at the edge, reducing latency and dependency on central systems.[/li][li]PLC Integration: Act as communication masters or data concentrators for networks of PLCs controlling specific processes (inlet works, biological treatment, clarification, disinfection, sludge handling).[/li][li]Optimization: Run advanced process control (APC) or AI/ML models for energy optimization, chemical usage reduction, and predictive maintenance.[/li][/ul][/li][li]Remote Monitoring & Connectivity:[/li][li][ul][li]Communication Gateway: Feature multiple industrial communication ports (Ethernet, Serial RS-232/485, CANbus) and support for protocols (Modbus TCP/RTU, PROFINET, EtherNet/IP, OPC UA) to connect PLCs, instruments, drives, and other subsystems.[/li][li]Remote Access: Enable secure remote monitoring and troubleshooting by engineers and management via VPNs or secure cloud platforms, reducing on-site visits.[/li][li]Cloud/Data Center Integration: Transmit critical data to central servers or cloud platforms for historical analysis, regulatory reporting, and enterprise-level visibility.[/li][/ul][/li][li]Specific Application Areas within an STP:[/li][li][ul][li]Inlet Works & Preliminary Treatment: Monitoring screens, grit removal, flow equalization tanks.[/li][li]Biological Treatment (Aeration Tanks, MBRs): Controlling air blowers (based on DO), mixers, internal recirculation. Monitoring MLSS.[/li][li]Secondary Clarification: Monitoring sludge blanket level, controlling RAS/WAS pumps.[/li][li]Tertiary Treatment (Filtration, Disinfection): Controlling filter backwash cycles, chemical dosing (chlorine, UV intensity).[/li][li]Sludge Handling (Thickeners, Digesters, Dewatering): Monitoring tank levels, temperatures, biogas production, controlling pumps and dewatering equipment.[/li][li]Pump Stations (Lift Stations): Remote monitoring and control of pumps, wet well levels, and alarms.[/li][li]Effluent Monitoring: Hosting final effluent quality analyzers and flow meters for compliance reporting.[/li][li]Odor Control Systems: Monitoring and controlling scrubbers or biofilters.[/li][/ul][/li][li]Reporting & Compliance:[/li][li][ul][li]Data Logging: Securely store vast amounts of historical process data required for regulatory compliance (EPA, local authorities).[/li][li]Report Generation: Automate the creation of daily, weekly, and monthly operational and compliance reports.[/li][li]Audit Trail: Maintain secure records of operator actions, alarms, and process changes.[/li][/ul][/li][/ol]Key Benefits for Sewage Treatment Plants:
[ul][li]Reduced Downtime: High reliability minimizes unplanned outages that can lead to overflows or permit violations.[/li][li]Improved Process Efficiency & Quality: Real-time data and control enable optimization, leading to better effluent quality and lower operational costs (energy, chemicals).[/li][li]Enhanced Regulatory Compliance: Accurate, reliable data logging and reporting simplify meeting stringent environmental regulations.[/li][li]Lower Total Cost of Ownership (TCO): Longer lifespan, reduced maintenance, and fewer failures compared to commercial hardware offset the higher initial cost.[/li][li]Increased Safety: Remote monitoring reduces the need for personnel in hazardous areas. Early fault detection prevents catastrophic failures.[/li][li]Scalability & Flexibility: Modular IPCs can be easily added or upgraded as plant processes or monitoring needs evolve.[/li][/ul]In essence, Industrial PCs are the rugged, intelligent brains of modern sewage treatment plants, enabling reliable, efficient, automated, and compliant operation in an environment that would rapidly destroy standard computing equipment. They transform raw data into actionable insights for optimal plant performance.
https://www.sinsmarts.com/4u-rackmou...t-pc-computer/
[ol][li]Environmental Resilience - Core Advantage:[/li][li]Dust & Particulate Protection (IP65/IP67): Sealed enclosures prevent ingress of dust, grit, and airborne fibers prevalent in STPs, especially near screens, grit chambers, and drying beds.[/li][li][ul][li]Humidity & Corrosion Resistance: Protected against high humidity, condensation, and corrosive gases (e.g., H2S) using conformal coatings, stainless steel housings, or specialized materials. Prevents short circuits and component degradation.[/li][li]Wide Temperature Tolerance (-20°C to 60°C+): Operates reliably in unheated pump houses, hot control rooms, and outdoor enclosures without climate control.[/li][li]Vibration & Shock Resistance: Withstands constant vibrations from pumps, blowers, and heavy machinery, using solid-state components (SSDs) and ruggedized construction.[/li][li]Chemical Splash Resistance: Resists damage from accidental spills of chemicals used in treatment (coagulants, disinfectants, pH adjusters).[/li][/ul][/li][li]Continuous Operation & Reliability:[/li][li][ul][li]Fanless Design: Eliminates the primary point of failure (fans clogged by dust/humidity) and allows silent operation. Passive cooling via heatsinks or chassis dissipation.[/li][li]Industrial-Grade Components: High-quality capacitors, power supplies, and motherboards designed for long-term, stable operation under load (24/7/365).[/li][li]Extended Product Lifecycles: Components are available and supported for 5-10+ years, ensuring system stability and reducing costly re-engineering.[/li][/ul][/li][li]Data Acquisition & SCADA/HMI Hosting:[/li][li][ul][li]Sensor Interface Hub: Connect directly to a vast array of sensors monitoring:[/li][li][ul][li]Flow rates (influent, effluent, between processes)[/li][li]Level (tanks, clarifiers, wet wells)[/li][li]Pressure (pump discharge, filter beds)[/li][li]Water Quality (pH, DO, ORP, Conductivity, Turbidity, TSS, Ammonia, Nitrate, Phosphate - often via analyzers)[/li][li]Equipment Status (pump on/off, valve position, motor load)[/li][/ul][/li][li]SCADA System Host: Run the core SCADA software that aggregates data from all PLCs and RTUs across the plant, providing central monitoring and control.[/li][li]HMI (Human-Machine Interface): Serve as the operator's workstation, displaying real-time process graphics, trends, alarms, and allowing manual control interventions. Often mounted near process areas or in control rooms.[/li][/ul][/li][li]Process Control & Automation:[/li][li][ul][li]Local Control Logic: Execute complex control algorithms (e.g., aeration control based on DO, chemical dosing based on flow and pH/turbidity) at the edge, reducing latency and dependency on central systems.[/li][li]PLC Integration: Act as communication masters or data concentrators for networks of PLCs controlling specific processes (inlet works, biological treatment, clarification, disinfection, sludge handling).[/li][li]Optimization: Run advanced process control (APC) or AI/ML models for energy optimization, chemical usage reduction, and predictive maintenance.[/li][/ul][/li][li]Remote Monitoring & Connectivity:[/li][li][ul][li]Communication Gateway: Feature multiple industrial communication ports (Ethernet, Serial RS-232/485, CANbus) and support for protocols (Modbus TCP/RTU, PROFINET, EtherNet/IP, OPC UA) to connect PLCs, instruments, drives, and other subsystems.[/li][li]Remote Access: Enable secure remote monitoring and troubleshooting by engineers and management via VPNs or secure cloud platforms, reducing on-site visits.[/li][li]Cloud/Data Center Integration: Transmit critical data to central servers or cloud platforms for historical analysis, regulatory reporting, and enterprise-level visibility.[/li][/ul][/li][li]Specific Application Areas within an STP:[/li][li][ul][li]Inlet Works & Preliminary Treatment: Monitoring screens, grit removal, flow equalization tanks.[/li][li]Biological Treatment (Aeration Tanks, MBRs): Controlling air blowers (based on DO), mixers, internal recirculation. Monitoring MLSS.[/li][li]Secondary Clarification: Monitoring sludge blanket level, controlling RAS/WAS pumps.[/li][li]Tertiary Treatment (Filtration, Disinfection): Controlling filter backwash cycles, chemical dosing (chlorine, UV intensity).[/li][li]Sludge Handling (Thickeners, Digesters, Dewatering): Monitoring tank levels, temperatures, biogas production, controlling pumps and dewatering equipment.[/li][li]Pump Stations (Lift Stations): Remote monitoring and control of pumps, wet well levels, and alarms.[/li][li]Effluent Monitoring: Hosting final effluent quality analyzers and flow meters for compliance reporting.[/li][li]Odor Control Systems: Monitoring and controlling scrubbers or biofilters.[/li][/ul][/li][li]Reporting & Compliance:[/li][li][ul][li]Data Logging: Securely store vast amounts of historical process data required for regulatory compliance (EPA, local authorities).[/li][li]Report Generation: Automate the creation of daily, weekly, and monthly operational and compliance reports.[/li][li]Audit Trail: Maintain secure records of operator actions, alarms, and process changes.[/li][/ul][/li][/ol]Key Benefits for Sewage Treatment Plants:
[ul][li]Reduced Downtime: High reliability minimizes unplanned outages that can lead to overflows or permit violations.[/li][li]Improved Process Efficiency & Quality: Real-time data and control enable optimization, leading to better effluent quality and lower operational costs (energy, chemicals).[/li][li]Enhanced Regulatory Compliance: Accurate, reliable data logging and reporting simplify meeting stringent environmental regulations.[/li][li]Lower Total Cost of Ownership (TCO): Longer lifespan, reduced maintenance, and fewer failures compared to commercial hardware offset the higher initial cost.[/li][li]Increased Safety: Remote monitoring reduces the need for personnel in hazardous areas. Early fault detection prevents catastrophic failures.[/li][li]Scalability & Flexibility: Modular IPCs can be easily added or upgraded as plant processes or monitoring needs evolve.[/li][/ul]In essence, Industrial PCs are the rugged, intelligent brains of modern sewage treatment plants, enabling reliable, efficient, automated, and compliant operation in an environment that would rapidly destroy standard computing equipment. They transform raw data into actionable insights for optimal plant performance.
0
4
0
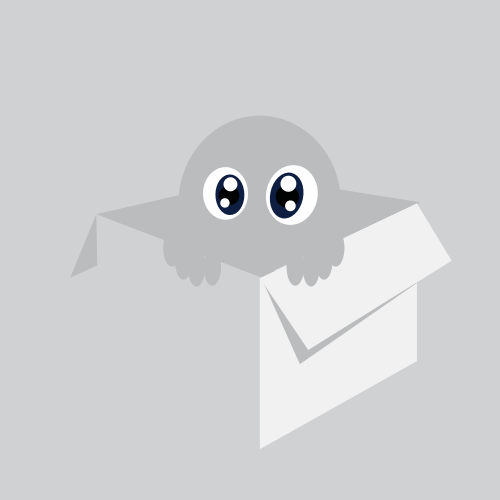
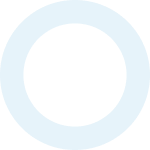
Komentar yang asik ya
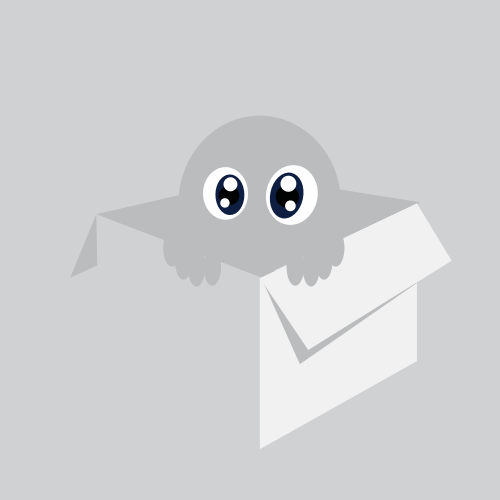
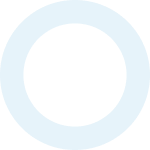
Komentar yang asik ya
Komunitas Pilihan