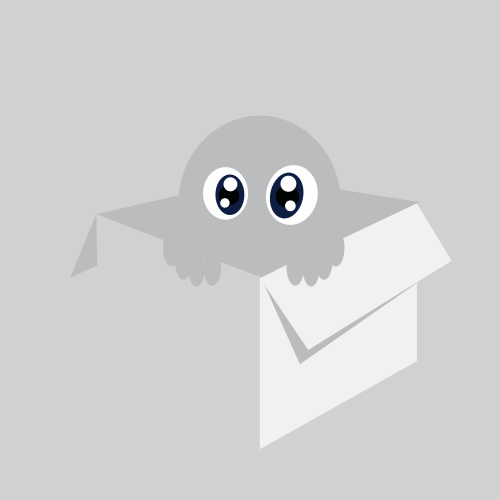
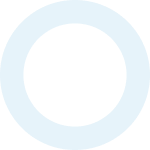
TS
arbazkhand84025
What is casting manufacturing
Casting manufacturing is a process used to create a wide range of parts and components, including everything from engine blocks and gears to decorative ornaments and jewelry. It involves pouring a molten material into a mold to create the desired shape, allowing it to cool and solidify, and then removing the finished product from casting manufacturer
There are several different types of casting manufacturing processes, each with its own advantages and disadvantages depending on the specific application. Some of the most common methods include sand casting, die casting, investment casting, and centrifugal casting.
Sand casting is one of the oldest and most widely used methods, in which a pattern is created and then used to make a mold out of sand. Molten metal is poured into the mold, and after it cools, the sand is broken away to reveal the finished part.
This method is relatively inexpensive and versatile, making it suitable for both large and small production runs.
Die casting, on the other hand, is a high-volume process used to produce large quantities of parts with consistent quality. In this method, molten metal is forced under high pressure into a metal mold, or die, which is then cooled and opened to remove the finished part.
Die casting is ideal for creating complex shapes with high dimensional accuracy, and it is often used in the automotive and aerospace industries.
Investment casting, also known as lost-wax casting, is a precision method used to create parts with very fine details and intricate shapes. In this process, a wax pattern is created and coated with a ceramic shell, which is then heated to melt the wax and harden the ceramic.
Molten metal is poured into the shell, and after it cools, the ceramic is broken away to reveal the finished part.
Centrifugal casting is a process used to create cylindrical parts, such as pipes and tubes. In this method, molten metal is poured into a spinning mold, and the centrifugal force pushes the metal outward to fill the mold.
This creates a part with a consistent wall thickness and high structural integrity.
Regardless of the specific method used, casting manufacturing offers several advantages over other manufacturing processes. It allows for the creation of complex shapes with high dimensional accuracy, and it can produce parts with a wide range of sizes and materials.
Additionally, casting manufacturing is often more cost-effective than other methods, especially for large production runs.
However, there are also some limitations and challenges associated with casting manufacturing. The process can be time-consuming, especially for larger and more complex parts, and it may require additional post-processing steps, such as machining or finishing, to achieve the desired surface finish and tolerances.
Casting manufacturing can also be affected by factors such as porosity, shrinkage, and other defects, which can impact the quality and integrity of the finished product.
Overall, casting manufacturing is a versatile and widely used process that offers many benefits for a variety of applications. Whether you need to produce large quantities of high-precision parts or create custom designs with unique shapes and materials, casting manufacturing can provide a cost-effective and reliable solution.
There are several different types of casting manufacturing processes, each with its own advantages and disadvantages depending on the specific application. Some of the most common methods include sand casting, die casting, investment casting, and centrifugal casting.
Sand casting is one of the oldest and most widely used methods, in which a pattern is created and then used to make a mold out of sand. Molten metal is poured into the mold, and after it cools, the sand is broken away to reveal the finished part.
This method is relatively inexpensive and versatile, making it suitable for both large and small production runs.
Die casting, on the other hand, is a high-volume process used to produce large quantities of parts with consistent quality. In this method, molten metal is forced under high pressure into a metal mold, or die, which is then cooled and opened to remove the finished part.
Die casting is ideal for creating complex shapes with high dimensional accuracy, and it is often used in the automotive and aerospace industries.
Investment casting, also known as lost-wax casting, is a precision method used to create parts with very fine details and intricate shapes. In this process, a wax pattern is created and coated with a ceramic shell, which is then heated to melt the wax and harden the ceramic.
Molten metal is poured into the shell, and after it cools, the ceramic is broken away to reveal the finished part.
Centrifugal casting is a process used to create cylindrical parts, such as pipes and tubes. In this method, molten metal is poured into a spinning mold, and the centrifugal force pushes the metal outward to fill the mold.
This creates a part with a consistent wall thickness and high structural integrity.
Regardless of the specific method used, casting manufacturing offers several advantages over other manufacturing processes. It allows for the creation of complex shapes with high dimensional accuracy, and it can produce parts with a wide range of sizes and materials.
Additionally, casting manufacturing is often more cost-effective than other methods, especially for large production runs.
However, there are also some limitations and challenges associated with casting manufacturing. The process can be time-consuming, especially for larger and more complex parts, and it may require additional post-processing steps, such as machining or finishing, to achieve the desired surface finish and tolerances.
Casting manufacturing can also be affected by factors such as porosity, shrinkage, and other defects, which can impact the quality and integrity of the finished product.
Overall, casting manufacturing is a versatile and widely used process that offers many benefits for a variety of applications. Whether you need to produce large quantities of high-precision parts or create custom designs with unique shapes and materials, casting manufacturing can provide a cost-effective and reliable solution.
0
197
0
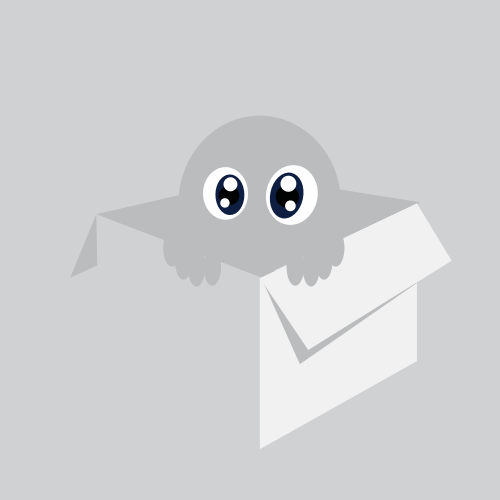
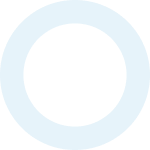
Komentar yang asik ya
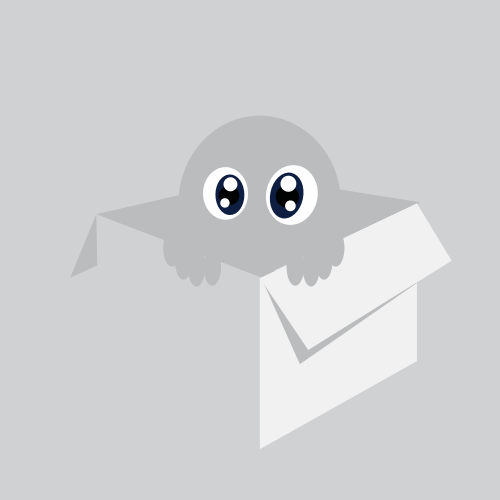
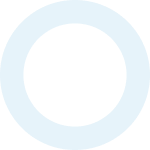
Komentar yang asik ya
Komunitas Pilihan